How Formlabs 3D Printers can help lower your golf scores
GolfMagic takes a closer look at the unique partnership between TaylorMade and Formlabs' 3D printers...

One of TaylorMade’s latest creations, the SIM fairway wood, represents continued improvements to ball speed and provides higher consistency for players. But did you know it was made using Formlabs’ 3D printers?
Incorporating 3D printing into the design process enabled engineers to completely redesign the club's appearance, highlighting how 3D printing can result in products that enhance consumer performance.
For more than 40 years, TaylorMade has been earning a spot in the best players' bags by delivering on its promise to create the best performing golf products in the world.
From beginners looking to improve their game to PGA Tour professionals seeking an extra edge, TaylorMade is driven by product innovation to make all golfers better.
The result? Some of the greatest golf clubs in the sport.
"Tiger Woods has the highest standards," said Chris Rollins, TaylorMade product development engineer.
"He is the most demanding player in the game, he inspects every inch of the club. The fact TaylorMade earned a spot in his bag, that is our greatest accomplishment."
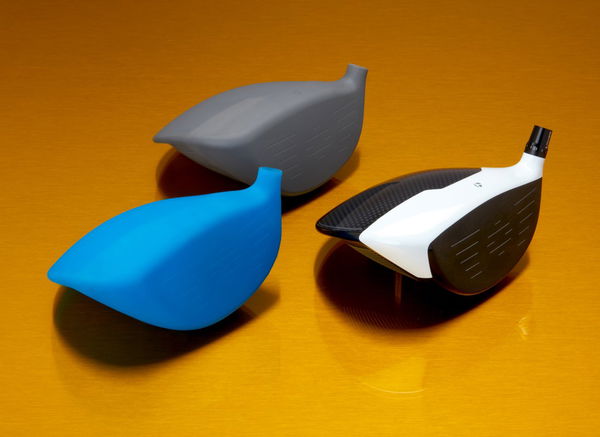
In 1979, the TaylorMade Pittsburgh Persimmon metalwood radically changed modern golf.
The first widely adopted metalhead driver was a major improvement over the wood-head drivers of the time, allowing players to drive the ball farther than ever before.
This product put TaylorMade firmly on the map, but staying there would require a true dedication to innovation and player performance.
Some 40 years later, when players enter a store and see the TaylorMade logo on a club, they know the same vision and love of the game that went into the original metalwood continues to permeate each new design.

In 2020, the new SIM fairway wood constitutes the very best of TaylorMade.
Pushing what is possible in club design, this club represents continued improvements to ball speed, higher launch, and most importantly, increased forgiveness for all players.
Designing a new club starts with brainstorming various innovations the team thinks they can pull off, and which core problems those innovations will solve.
When creating the SIM fairway wood, the company wanted to find new ways to lower the centre of gravity, improve turf interaction, and create a more forgiving face.
Engineers went to work on creating a new head from scratch, starting with 2D designs and performance analysis.
The goal was to redesign how weights are inserted into the club head, boosting performance on each swing. Without having to worry about prototyping cost, the team fired up their in-house 3D printers to bring CAD files to life.
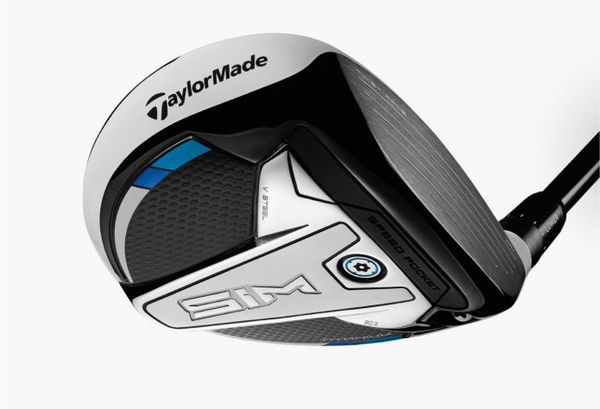
Working in 3D space is vital for TaylorMade so they can physically feel and see how different weight distributions and designs alter the club head.
The SIM fairway’s radical new look is a direct result of this process, and the outcome is a striking new look with new performance benchmarks for players.
The team uses Draft Resin to quickly print new parts in a few hours, while switching to Grey Resin for looks-like prototypes.
Masking the topline onto prototypes of Grey Resin heads has become a major advantage to designers thanks to the high quality plastics available on the Formlabs 3D printer.
"It’s always exciting to see how Formlabs’ users leverage our technology to create new and inventive things," said Jennifer Milne, Formlabs product marketing lead.
"TaylorMade’s use of our proprietary resins for its SIM fairway highlights the importance of how we make things and what they are made of, and is a great example of how different industries are embracing 3D printing to improve workflows, R&D, and their end products.
"The materials we create for our 3D printers elevate the product development of everything from golf clubs to dentures so the end-user can have the best experience possible."
The ability to perfectly mate parts together is another standout feature of Grey Resin, and something engineers couldn’t find when shopping for other in-house printers.
Mating 3D printed parts allowed the team to test multiple new shapes for the weighted sole plates inserts on the SIM fairway wood, ultimately creating a better club.
For TaylorMade engineers, the printing materials wound up being the biggest asset in their quest to make a better fairway wood.
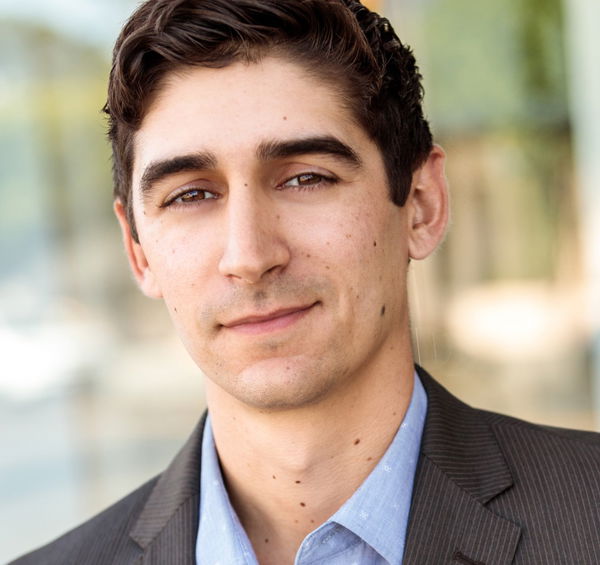
"From the moment we received our first sample parts from Formlabs we knew we needed to shift gears in our printing department," said Rollins.
"Better, faster and cheaper is a rare package in the engineering world and made purchasing a Form 2 an easy sell. Specifically, the resolution and texture of the Grey Pro material allowed our industrial design team to mask, paint, and decal heads better than our previous prints.
"The clarity of Grey Pro allowed me to hone performance attributes like address shape, scorelines, and topline.
"My initial focus was on metalwoods, but within a year of purchasing, we had 3D printed experiments pop up across the iron, putter, wedge, and ball teams."
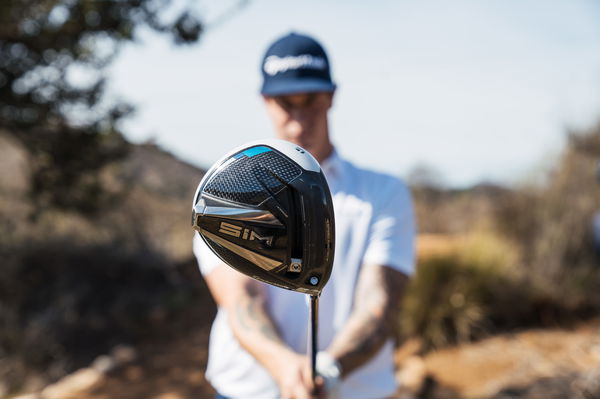
So will 3D printing continue to be used on future TaylorMade clubs? You bet.
"It is safe to say that TaylorMade is just getting started with 3D printed applications," said Rollins.
"It's way too fast, too cheap, and allows us to hone into the details like never before.
"We have some really pushing edge projects in the works involving 3D printing, and golfers are going to love it."
Watch this space.
For more information, please visit www.formlabs.com and www.taylormadegolf.co.uk
Sponsored Posts
Latest News
![Lexi Thompson [Instagram]](https://cdn.golfmagic.com/2025-04/le122.jpg?width=400)